Since 1993
PushCorp is a robotic tooling manufacturer, specializing in material-removal equipment. As inventors of the force compliance device, we have helped automate thousands of robotic processes across the globe. Innovation is in our DNA, and it’s why we are constantly evolving, creating, and adding new surface-finishing products to our portfolio each year. Whether you are a manufacturer or a robotic systems integrator, we have the tooling to help automate your manual process. Let's discuss your project and see how we can help bring quality and consistency to your surface-finishing application.
The First Robotic Force Compliance Device
PushCorp was founded in March 1993 with the primary goal of creating end effectors for robotic, surface-finishing processes. Our first product, which was patented in 1995, was the Adjustable Force Device (AFD). This product's function was to allow a robot to maintain a consistent yet adjustable force when in contact with a part's surface. Previously, industrial robots simply moved from point A to point B without any regard for the amount of force being applied. PushCorp’s innovative compliance device opened the door for robotic grinding, sanding, polishing, and other surface-finishing applications that require a precise force. Prior to this invention, these types of processes were considered virtually impossible to automate due to the immense programming that was required to account for inconsistencies between parts and the abrasive wear.
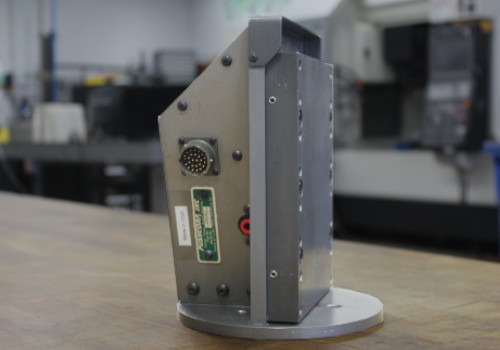
PushCorp's First Robotic Spindle
The innovation didn’t stop there; after selling the first AFD systems, it became apparent that there was a lack of rotary spindles that could be mounted on the compliance device. In the late '90s, most of the spindles on the market were very heavy, since they were designed for CNC’s and other fixed automation machines. On the other hand, there was a plethora of pneumatic tools; however, these were not robust enough for robotic, surface-finishing applications. These pneumatic tools would slow down when they came in contact with the part or when there was a drop in air pressure. Both of these factors contributed to inconsistent surface finishes. PushCorp solved the weight and consistency issues with our revolutionary servo spindle, which was released in 1997. The liquid-cooled, permanent magnet servo spindle was not only lightweight, but also provided a high power-to-weight ratio and constant speed, enabling consistent material removal.
Manufactured in the USA
At our core, there has always been an emphasis on quality and durability across PushCorp's entire product line. Being heavily involved in the automotive and aerospace industries, our customers expect a product that can last years with continuous, trouble-free use. To ensure this high level of quality, a decision was made early on to manufacture and assemble as many products in-house as possible. To this day, 95% of all our components are machined in our state-of-the-art manufacturing facility in Dallas, Texas. With a full range of CNC and measuring equipment, we are able to manufacture extremely high quality parts for new tools, repairs, and R&D projects. We also machine custom brackets and tool holders to make integrating our equipment with your robot and abrasives easier than ever before.
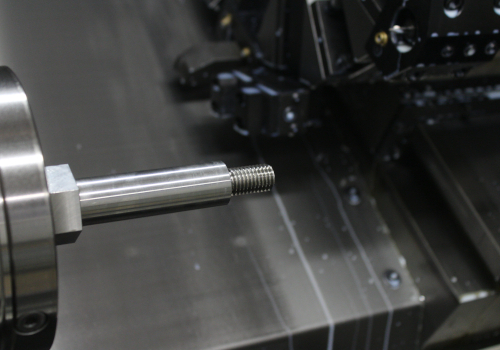
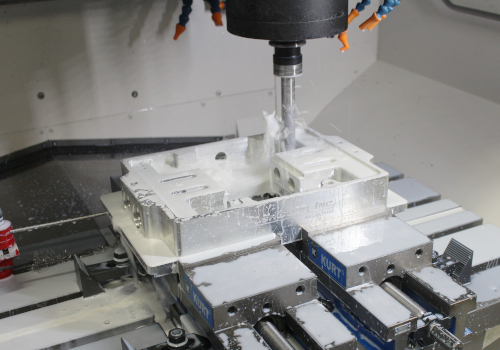
Hand-Assembled, Robotic Tooling
Today, PushCorp can proudly say that 100% of assembly takes place in- house. Each product is hand assembled with rigorous quality control procedures to ensure a premium and unsurpassed end product. PushCorp has several production areas, which are outfitted with custom, dedicated tooling to ensure efficiency and consistency in the assembly process.
Exceptional Quality Control
Quality control is at the center of everything we do at PushCorp. As a company, we have dedicated countless engineering hours to create testing equipment for all of our force compliance devices and servo spindles. For robotic polishing and sanding applications, precise force is critical. We use fixture plates and calibrated external load cells to test our AFD compliance units after assembly. Unlike our competitors’ products, our equipment does not need to be routinely re-calibrated. With reasonable care, the force compliance device can apply consistent and accurate force for many years.
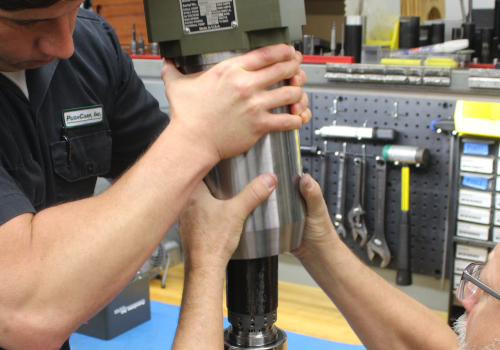
As with all of our products, if a tool is damaged, we can rebuild the equipment to like-new condition. Only then would re-calibration be needed. Likewise, our servo spindles have an entire room dedicated to quality control. Before each spindle is shipped, we run them for the suggested break-in period recommended by the bearing manufacturer. This not only breaks in the bearings but is another procedure we undergo to find components that have manufacturing defects. During this time, the temperature, noise, torque, and speed are measured, automatically. With this data, we are able to analyze the results to help pinpoint any potential issues and guarantee a quality product for our customers.

Robotic Process Labs to De-risk Automation Projects
With over 30 years of experience, we have helped provide tooling to integrators and end users to automate thousands of robotic, material-removal applications. In Dallas, Texas, we have two state-of-the-art labs dedicated to proof-of-concept testing to help de-risk your project. Big or small, our application engineers are ready to help process your parts and narrow down the equipment needed for a successful system. For this service, we recommend sending a defined number of unfinished parts (depending on part complexity and size) and one finished part; from there, we will use our full arsenal of material-removal end effectors to recreate your manual process and recommend the tooling and abrasives that you will need to automate. At the end of the testing, we will provide a video showing our equipment in action as well as a full report of the parameters we used to achieve the surface finish. Whether this is your first time to integrate our equipment or you are unsure of the surface finish our tooling can achieve, reach out today and schedule a proof-of-concept demo.