Robotic Deflashing
Automation Applications
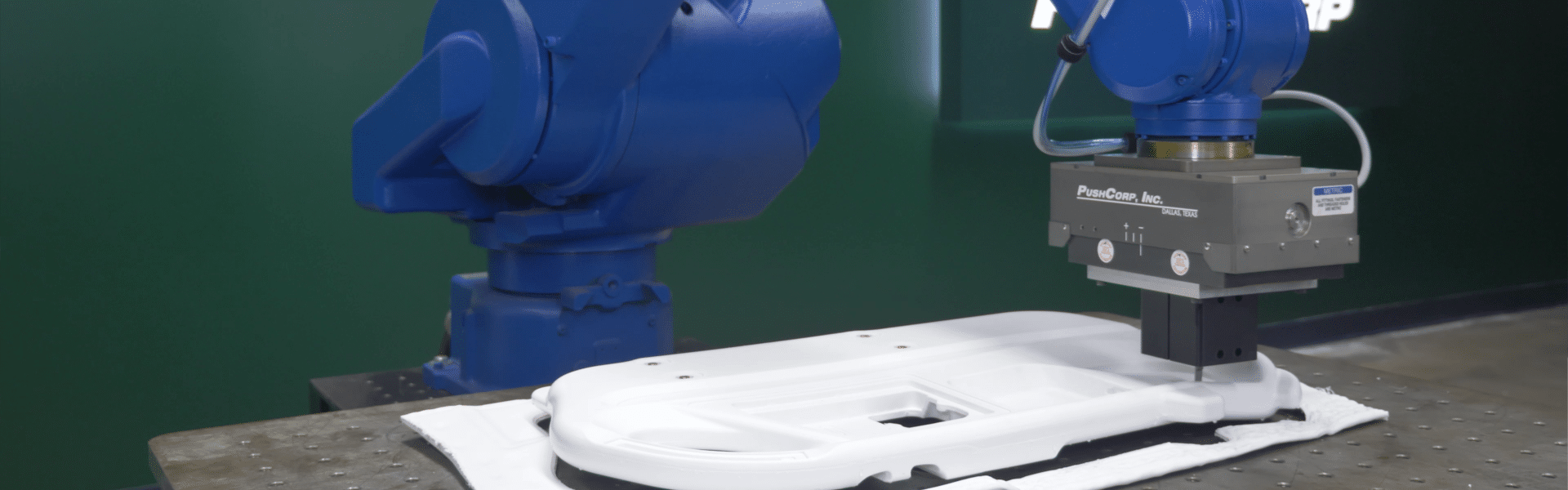
Deflashing
Precise Force and Constant Contact
Deflashing is a material-removal process that removes the "flash" after a part comes out of a mold. This can occur when a mold is worn out or the part’s geometry is very complex, so the viscous material seeps from the cavity. This can be seen with both metal and plastic parts, so the process to remove this material can be quite different.
For plastic parts, these often come out of the mold still hot and can be cut with a knife. If the parts are not immediately processed and the material cools down, then it is common for companies to use a spindle and an end mill to remove the flash via a machining process.
For aluminum and softer metals, the same approach can be taken, but a larger spindle with heavy-duty bearings is necessary. Due to the nature of the molding process, the flash can be inconsistent in shape and thickness. As a result, the bearings need to have a high radial load to help withstand interrupted cuts, varying thickness, and vibration from the process.
For harder materials such as steel or ductile iron, the heavy-duty spindle is also used, but it is paired with cutoff wheels or diamond coated abrasives (ductile iron only).
No matter what the material is, these applications are dirty, dangerous, and dull. They require very sharp cutting tools or abrasives that can be harmful if they come in contact with a human operator. As a result, manufacturers are quickly moving to automated deflashing processes. Not only does this create a safer work environment, but also results in a higher quality part.
Robotic Deflashing Plastic Part
As an illustration, this video shows how effortless automated robotic deflashing can be. In fact, a robot paired with a PushCorp force compliance device is just what you need to automate your robotic, plastic deflashing application
This video showcases our AFD72. It enables the sharp knife to remain in contact with the parent material without damaging the substrate.
There are two key elements to this process. First, the AFD72 maintains constant contact with the surface. Then, the constant force allows the sharp knife to follow the contour of the part without digging in and damaging the final product.
We recommend:
Automated, Robotic Deflashing on Composite Panels
What Are You Waiting For? Get in Touch With Our Application Engineers Today! With 1000’s of systems sold, we have the equipment needed to make your project a success. Our application engineers are ready to learn about your process and help recommend the right products for your robotic surface finishing system.
With 1000’s of systems sold, we have the equipment needed to make your project a success. Our application engineers are ready to learn about your process and help recommend the right products for your robotic surface finishing system.