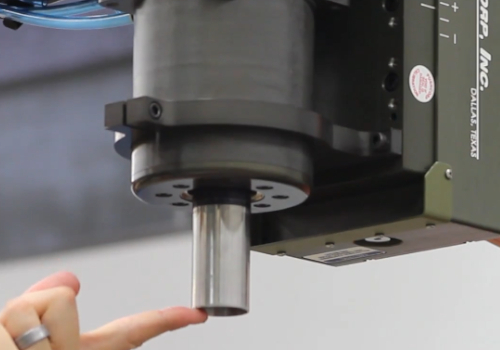
Force Control Tooling to Give Robots a Human Touch
Knowing where to start is often the hardest part of a robotic automation project. For robotic, surface-finishing applications, it is critical to understand what equipment is needed in order to achieve your desired surface finish. PushCorp equipment has a wide range of robotic, material-removal tooling that enables a robot to emulate a “human touch.” Our equipment ensures a manufacturing robot can apply a constant force to bring an unmatched level of consistency and precision for robotic sanding, grinding, polishing, and many other material-removal applications.
What is a Force Control Device?
PushCorp force control devices, also known as force compliance devices, allow a robot to maintain a consistent yet adjustable force when in contact with a part’s surface. A standard industrial robot moves from point A to point B without any regard for the amount of force it is applying. When attached to a robot arm, our devices’ sliding carriage allows whatever tool is attached to maintain contact with the part’s surface with a specific force. Unlike force torque sensors and through-the-arm compliance, our device does not have to compensate for the mass of the robot arm. This makes our equipment more accurate, precise, and easier to use than any other force compliance product on the market.
What Is The Difference Between Active Vs. Passive Force Compliance?
Active Compliance devices apply consistent force in any orientation, automatically. Just tell it what force you want and an active tool will apply it up, down, sideways or any orientation in between. This makes it a great candidate for parts with curved surfaces.
Passive devices rely on external, customer-supplied air pressure regulators to set the applied force. They work extremely well for less demanding operations, flat or prismatic parts, or more specialized processes like Weld Shaving, where high-accuracy force control is unnecessary.
LEARN MORE ABOUT OUR ROBOTIC FORCE COMPLIANCE TOOLING
Active Compliant Tools utilize internal, closed-loop feedback control along with internal force, acceleration, and position sensors to accurately apply the desired force to your part.
Passive Compliant Tools are simple, less-expensive, open-loop devices. For every new orientation, the supply pressure must change in order to maintain a specified force.
Servo Spindles
Designed For Robotic, Material-Removal Applications
PushCorp offers a wide range of powerful, rugged, and efficient electric spindles. All PushCorp spindles utilize liquid-cooled, permanent magnet, brushless, closed-loop servomotor technology. This technology gives our spindles the highest power-to-weight ratio and power efficiency in the industry, making them the ideal choice for robotic, material-removal applications. With proper cooling, our motors are designed to run with up to a 100% duty cycle – turn them on, leave them on. They can handle high-power, continuous operation.
Servo technology allows for continuously variable speed and constant, maximum torque over the entire speed range. Finally, all PushCorp spindles are designed to be easily mounted to our compliant tools in a variety of orientations to provide a complete, end-of-arm process solution.
Programming Beautiful Surface Finishes
PushCorp equipment, mounted to an industrial robot, makes programming easier than ever. Our force compliance devices have a linear stroke ranging from 20-40mm. This greatly reduces programming time since fewer points are needed over complex geometries. This makes programming robotic deburring, sanding, and grinding paths a breeze.
What is included in a System?
Whether you are an integrator or an end user, PushCorp supplies consumers with all of the components needed to implement a robotic, surface-finishing system. When purchasing a spindle and force compliance device, the following components come standard:
Our cables are high-flex, industrial cables designed specifically for robotic applications. These can be ordered either as a single cable or in segments. If you go with a single cable, you can order this with a maximum length of 30 meters. Also, the connectors that plug into the spindle can either be ordered with straight or 90 degree connections. If you would like segmented cables, we offer these in either 2 or 3 segments with a maximum total length of 30 meters.
PushCorp offers turn-key control panels that integrate the servo amplifier and the active force compliance controller into an easy-to-use control box. These utilize standard protocols to communicate with industrial robots. Whether you want to use EthernetIP, DeviceNet or ProfiNet, we have you covered. Spend less time wiring and more time programming with our turn-key control panels.