Technology Overview
Robotic Force Compliance Devices allow you to automate processes and give an industrial robot a "human" touch. Their sliding carriage allows the process equipment to maintain contact with a part's surface with a specific force. This technology is a closed-loop system that works independently of the robot arm. Unlike force torque sensors, our device does not have to compensate for the mass of the robot arm. Instead, we only deal with the weight on the end of the sliding carriage. This makes our robotic force compliance devices more accurate, precise, and easier to use than any other equipment on the market. This is critical when dealing with material-removal applications (grinding, sanding, deburring, weld shaving) where consistency is key to achieving a beautiful surface finish.
Active Technology
Automated Active Compliant Tools utilize internal, closed-loop feedback control, along with internal force, acceleration and position sensors, to accurately apply the desired force to your part. Accurate force is maintained over contours, in any orientation. Just tell it what force you want and an Active tool will apply it up, down, sideways or any orientation in between.
Passive Technology
Automated Passive Compliant Tools are simple, less-expensive, open-loop devices. They rely on external, customer-supplied air pressure regulators to set the applied force. While they may lack the ultra-high precision and flexibility of Active compliance, they work extremely well for less demanding operations, flat or prismatic parts, or more specialized processes like Weld Shaving where high-accuracy force control is unnecessary.
Parallel
When combining PushCorp’s spindle and force compliance devices, there are two ways they can be mounted. The first way is a parallel configuration. This is great setup when using media such as flap disks and DA sanders. The direction of compliance is parallel to the spindle, which can be seen in the animation. This video shows how a parallel setup can be used in a real world application.
Perpendicular
The second mounting option is a perpendicular configuration. This is great setup when using media such as bristle brushes or saw blades. The direction of compliance is perpendicular to the spindle, which can be seen in the animation. This video shows how a perpendicular setup can be used in a real world application.
Active Compliance
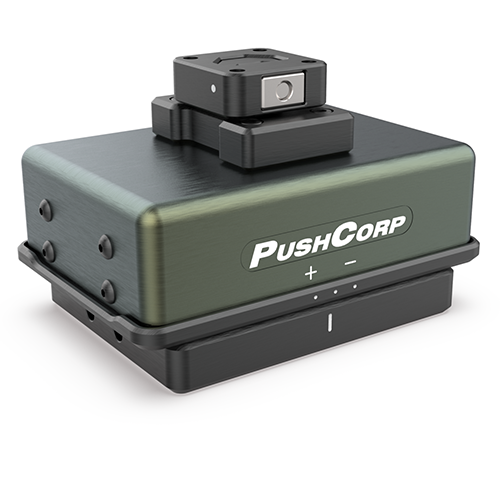
AFD120
AFD120 The AFD120 is part of PushCorp’s Active Compliance series, and has been designed with cobots and smaller industrial robots…
Learn More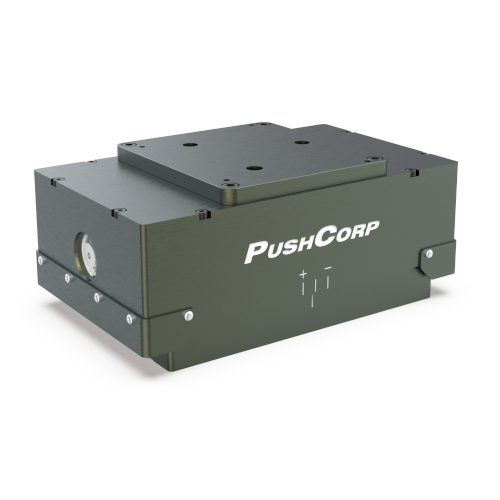
AFD310
AFD310 The AFD310 is part of PushCorp’s Active Compliance series. This end effector can apply up to 60 lbf [267 N]…
Learn More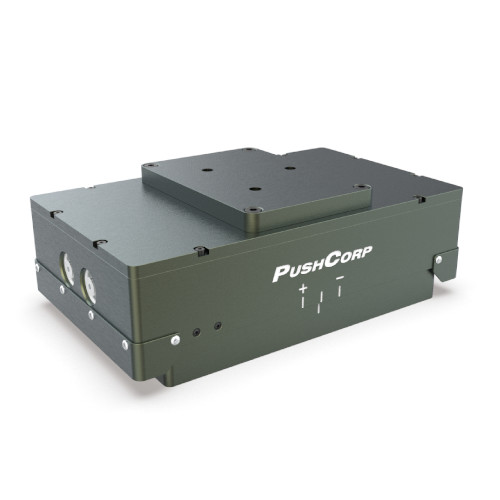
AFD620
AFD620 The AFD620 is part of PushCorp’s Active Compliance series. This end effector can apply up to 115 lbf [511 N]…
Learn More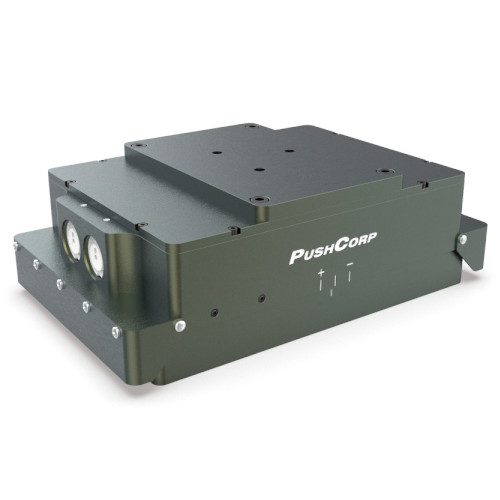
AFD1240
AFD1240 The AFD1240 is part of PushCorp’s Active Compliance series. This end effector can apply up to 215 lbf [956 N]…
Learn MoreActive Compliance Controller
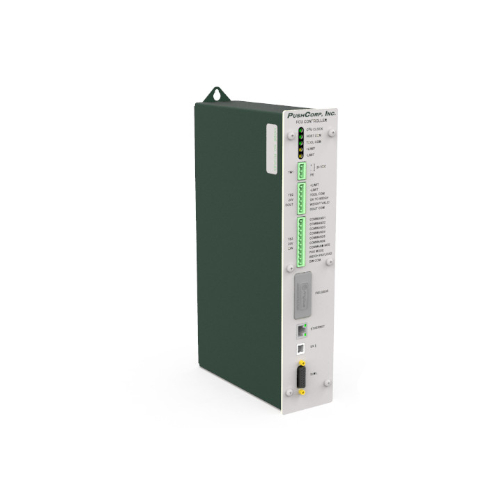
FCUFLEX
Active Compliance Force Controller The PushCorp FCUFLEX compliance controller, combined with PushCorp’s Active Compliance Force Devices, creates an integrated force control system unsurpassed by…
Learn MorePassive Compliance
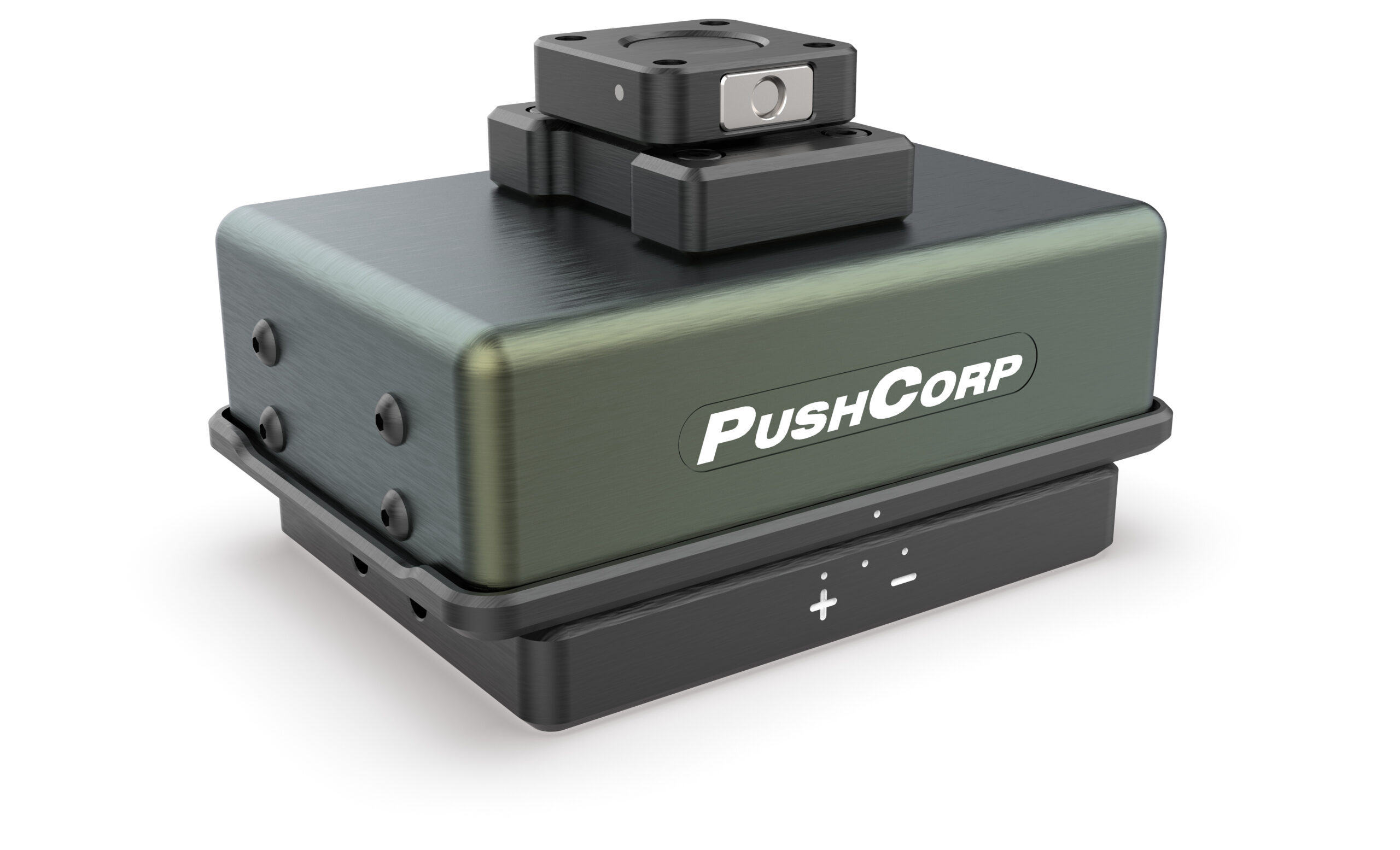
AFD62
AFD62 End Effector (EOAT) The AFD62 is part of PushCorp’s Passive Compliance series. This end effector can apply up to…
Learn More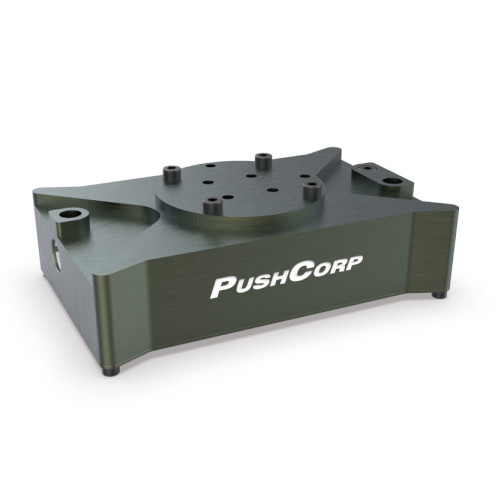
AFD52
AFD52 The AFD52 is part of PushCorp’s Passive Compliance series. This end effector can apply up to 8.0 lbf [37 N] in…
Learn More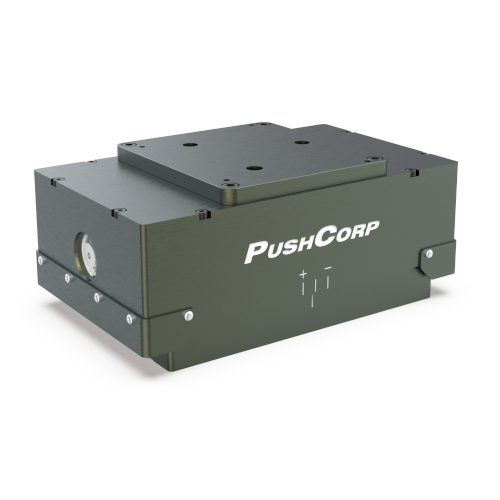
AFD72
AFD72 The AFD72 is part of PushCorp’s Passive Compliance series. This end effector can apply up to 60 lbf [267 N] in…
Learn More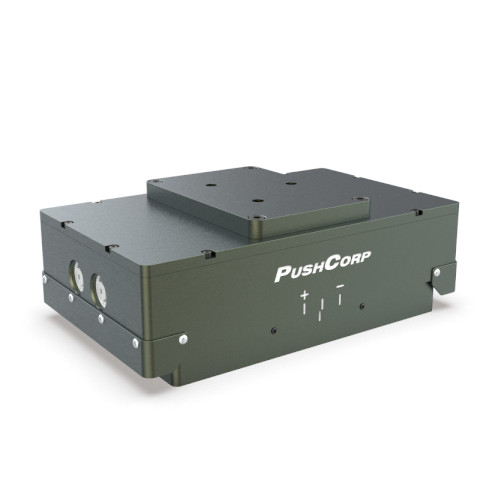
AFD82
AFD82 The AFD82 is part of PushCorp’s Passive Compliance series. This end effector can apply up to 115 lbf [511 N] in…
Learn More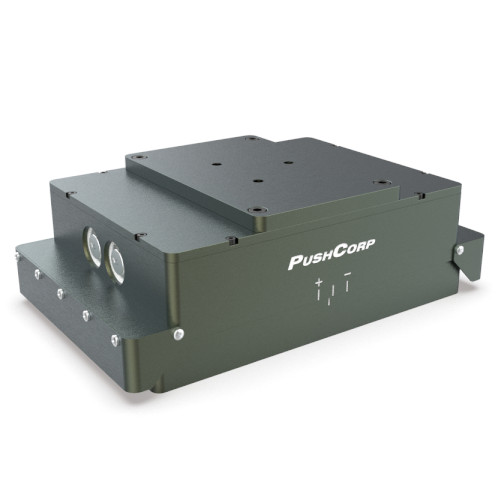
AFD92
AFD92 The AFD92 is part of PushCorp’s Passive Compliance series. This end effector can apply up to 215 lbf [956 N] in…
Learn More