High-Flex Robot Cables
PushCorp equipment comes standard with a set of High-Flex, Robotic Cables. These cables can be ordered at various lengths, clockings, and segments to provide customers with solutions that can be tailored to their robotic process. Both Feedback and Power cables are stranded in pairs and intended for flexible stresses. Their versatility and durability make them a perfect complement to our material-removal, end-of-arm tooling, which is designed to process parts in any orientation. In order to specify the correct cables, it is important to identify the various options available. The following sections will provide an overview of each PushCorp cable offering so you can select the ones that will best fit your application. Based on the cable, you can use the specifications below to determine cable diameter, bend radius, max temperature, and the certifications. For example, if the cable part number on your quote is 576G-811M14-943FG, the middle number “811″ is the part number for the cable.
SPECIFICATIONS
Cable Diameter | 1193 – 9.1 mm (.36 in) 811 – 7.6 mm (.30 in) 4684 – 6.6 mm (.26 in) 4936 – 7.7 mm (.30 in) |
Bend Radius | 1193 & 811 flexing ~ 7.5x cable ø fixed installation ~ 4x cable ø 4936 & 4684 |
Max Temp | flexing -20 °C to +80 °C (-4° t0 176 °F) fixed -40 °C to +80 °C (-40° to 176 °F) |
Certifications | RoHS |
Straight Connectors
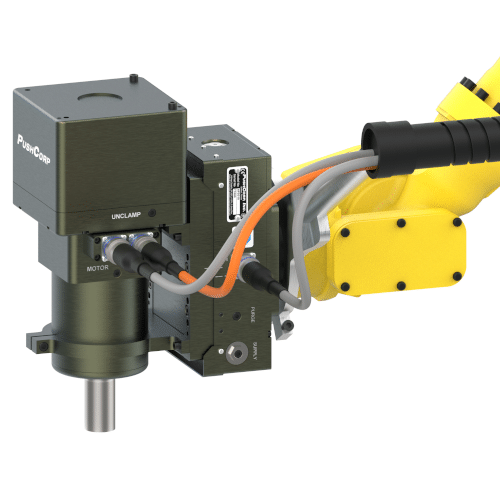
Our most popular cables have a straight connector with no bend. As shown in the following image, this orients the cables away from the motor and force compliance device housings. This design helps to ensure the cable has enough slack before it is routed back to the dress package. As a result, it can be great for applications that change orientations a lot and are not restricted by tight spaces.
90 Degree Connectors
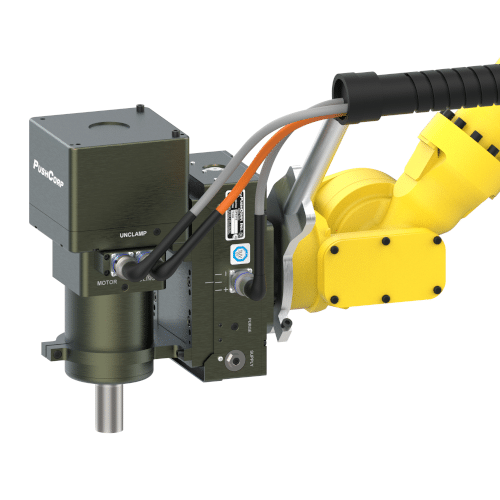
If your set-up requires a tighter or more compact solution, cables can be ordered with a 90 degree connector on the tool end. This orients the cables toward the motor and force compliance housings. This is beneficial for processes that need to fit in tight locations or cables that are at a higher risk of being snagged by the part. Since the cables have 90 degree connectors, you must specify the clocking for each. The following section will go into detail on this process.
Cable Clockings
Cable clockings are illustrated below. The orientation letters are spaced in 45 degree increments and correspond with the direction of the cable when plugged in. For example, a spindle cable with an “A” clocking will be pointed upwards at a 45 degree angle. A cable with the same orientation for a force compliance device (with the + side down) would be a “B” clocking.
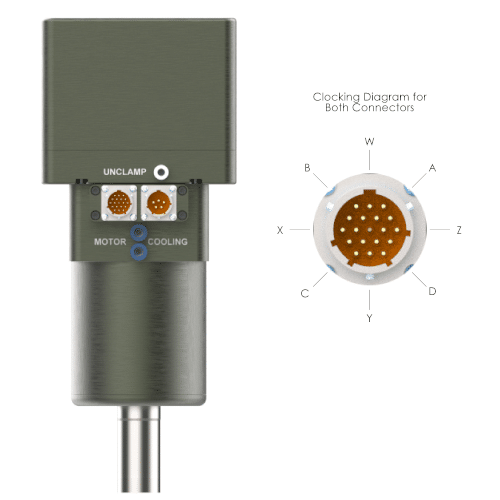
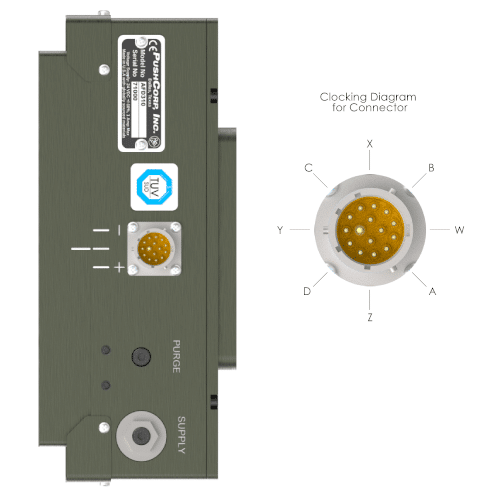
Cable Length and Segments
Cables can be ordered in a variety of lengths and segments. They are available in a maximum of 3 segments and with a total length of 30 meters. For example, a single segment can be up to 30 meters; two segments can be 15 meters each; or three segments can be 5 meters, 10 meters and 15 meters. We also offer cables shorter than 2 meters. These shorter cables are measured in inches and are available from 12 to 78 inches. The tolerance on the cables specified in inches will be -0 to +3″ and the cables specified in meters will be -0 to +.5m. The measurements for a cable with two straight connectors are taken from the face of each connector. For a cable with two 90 degree connectors, this measurement is taken from the center of each connector. If it has one straight and one 90 degree connector, the measurement will be taken from the face of the straight connector to the middle of the 90 degree connector. You can download the drawing showing the tolerances HERE.